Measuring temperature is one of the most common work performed during any industrial process. Like any other parameter, the effectiveness of their measurement depends on factors such as accuracy and the nature of the instrument, the speed in capturing the dimensions of the object in question and the distance between instrument and receiver. In the case of temperature measuring sensors, are fundamental tubes providing the necessary protection to electrical equipement and they are normally provided with an integrated compression fitting, valid for multiple manufacturing processes.
The connection between an industrial process, the measurable temperature and a thermometer requires the collation, screwed tightly or well-welded, of the compression fitting, in which the cap is attached to the thermometer that subsequently remains stable through a compression ring. Another aim of the compression fitting is to enable replacement of damaged probes without resorting to interrupt the process.
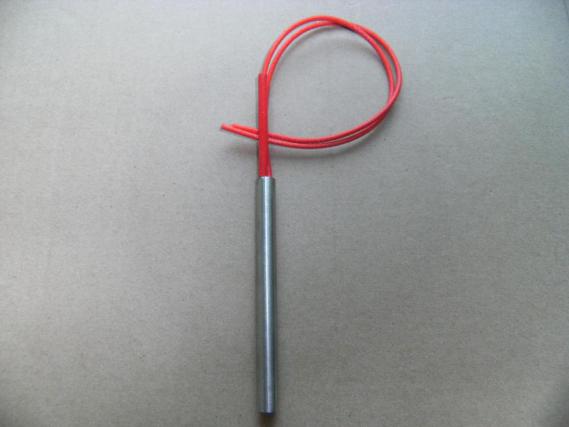
Furthermore, the fact that the capillary tubes are adapted to be welded to a fitting, also of stainless steel, it enables to fit thermometers or temperature sensors to any measuring system. Therefore, adaptability is another one of its strengths.
In resistance sensors, temperature is a factor that determines the electrical resistance being its room for maneuver between -200 and 600 °C, they are very stable and with an excellent accuracy. Those used mostly are Pt100 probes, which are manufactured in different formats:
– Winding wire in ceramics: sealed tubes at both ends containing platinum wire, with heat range up to 600 °C.
– Thin layer of platinum on a ceramic base: its advantages over the abovementioned are its smaller size and increased resistance to vibration, being valid for measurements not exceeding 500 °C.
Among the advantages of stainless steel capillary tubes, it is highlighted its excellent resistance to corrosion, pressure and mechanical traction and chemical action, as well as its biological inertia and the fact to ensure long product lifetime. These tubeswhose chemical resistance makes them tolerate very harsh environments, are able to emphasize higher strength in alloys of nickel, molybdenum, copper and silicon.
The stainless steel tubes are basic in branches of industries such as food, petrochemical, chemical, pharmaceutical, industrial cooling or related to the treatment of drinking and waste water, among many others, they require accurate and reliable information on, for example, temperature, pressure, level and flow volume in a point of the process. For these companies, the reliability of data, quality assurance and corrosion resistance are key values to choosing one or another solution.
Pyrometry in the most demanding conditions.
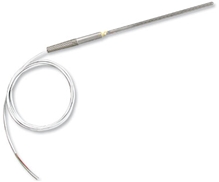
The measurement of data on temperature and also pressure in industrial environments is one of the most delicate processes that exist in industries such as chemical or food (the latter is noteworthy since the viticultural cellars to large corporations engaged in precooked food production).
Particularly in the food industry and alcoholic beverages production there is also an added commitment of health guarantee to the final consumer. The control requirement is even stronger.
In such environments, it is necessary to have available applications measurement and control in industrial facilities that provide a solution with high resistance to corrosion and abrasion caused both by the various chemical agents such as physical processes that are applied. The application of capillary steel tubes, besides protecting the instruments, allows reduction of variations in the temperature measurements.
In general, concerning the needs of measurement and control instrumentation for pyrometry, they are pursued complete solutions based on high quality components. Only by combining quality products with adaptability capacity and maximum reliability, it is possible to answer the needs of accurate and reliable data in the most committed and sophisticated industrial processes.